CNC MACHINE IN MECHANICAL
What is CNC turning?
CNC machining in mechanical engineering is a method of cutting materials based on the circular motion of the workpiece and the reciprocating motion of the cutter (vertical or horizontal). If turning machining is done on CNC lathes, it is called CNC turning.
In the past, turning machining was done on mechanical lathes, operated by human control. However, since the development of automation technology, the CNC latheswith integrated automatic control system, help the turning machining process to be done quickly and with higher accuracy, and at the same time can create out complex product details in a short time.
Machining on a CNC lathe simplifies all stages of round turning, taper turning, chamfering, grooving, face turning… The cutting tool used on a lathe is called a lathe.
Mean method characteristics
- Unlike milling, which involves the rotation of the tool and the stationary workpiece, in contrast, the turning method relies on the circular motion of the workpiece and the reciprocating motion of the cutting edge.
- The magnitude of the cutting speed V is basically based on the strength of the workpiece as well as the abrasion resistance and heat resistance of the cutting piece.
- Feed f is the distance traveled by the cutter in one revolution of the workpiece, rough turning uses large feeds, fine turning uses small feeds. Through the feed movement, the depth of cut is determined.
- Turning is mainly used to manufacture product parts with round shapes such as smooth shafts, taper, holes, eccentrics, etc.
- The turning tool is usually composed of a tool holder and a replaceable cutting piece. Usually, with different turning types, a compatible tool will be needed. Turning types in turning machining methods will be discussed later in this article.
- Currently, CNC turning machining greatly increases the accuracy and glossiness of product details and also helps to increase productivity in production.
What is coarse & fine turning?
Based on the level of perfection of product details, we have rough turning, semi-finishing, and thin turning.
Rough convenience
- Roughing is the process of peeling off the outer surface of the workpiece, in order to remove part of the ugly, convex workpiece surface as well as shape part of the shape of the product part and also detect defects. of the embryo.
- Cutting depth from 4-6mm.
- Lathes used for roughing need to achieve large capacity, high rigidity, accuracy is not too important when rough turning.
- Outer roughing can be cut in layers, segments or combined.
Convenience for sale
- The semi-finishing process is performed after rough turning and before finishing turning, in order to remove excessive rough steps on the part, to support the finishing turning process.
- Cutting depth from 2 to 4 mm.
Convenient
- Finishing is the final machining process for surface finishing, typically using turning tools with hard alloy or diamond blades to remove a relatively thin layer of metal from the surface of the part.
- In the cutting mode when fine turning, the amount of feed and depth of cut are quite small, and the cutting speed is quite large. The speed when turning aluminum alloy can reach from 1000 – 1500m/min, with copper alloy it is from 300 – 450 m/min, other metal is from 200 – 250m/min.
- Lathes used for the finishing process need high precision and rigidity.
Types of turning machining
According to the machining surface of the workpiece, the turning processing method is divided into the types of cylindrical turning (round turning), head turning (face turning), boring turning, cutting turning, slotting turning, etc. threading, shaping.
Turning the outer surface
This type of turning turning is used most often, by using the turning tool to work on the outer surface of the workpiece, mainly used to create cylindrical surfaces such as long cylindrical turning, horizontal cylindrical turning, wide finishing turning.
Convenience to naked face
A type of turning machining to create a surface perpendicular to the axis of rotation of the part, a layer of metal is removed from the top of the workpiece. This type of turning machining can use many different types of turning tools such as face-bladed knives, straight-headed knives, curved-headed knives, shoulder knives, etc.
Hole punching facility
Selected when it is necessary to make holes of different diameters and sizes for the part, usually this type of turning will be done on a special boring machine, lathe and using anti-vibration turning tools to ensure ensure the dimensional accuracy of the hole.
Convenient to cut off
A type of turning machining to remove a part of the excess workpiece or cut off the part from the workpiece axis. For this type of turning, a specialized tool with high durability is required.
Main lathe
As a type of turning machining for grooving on the product axis, the slotting tool performs a horizontal or vertical feed movement with the axis of rotation. There are three main types of groove turning: surface groove, outer groove, and inner groove.
Lace turning
With specialized threading tools, this type of turning helps to create threaded surfaces. Thread turning method is used quite commonly in mechanical processing, however, the productivity when turning thread is usually not high, especially when turning small hole or small thread pitch or the rigidity of the tool shaft is weak.
Shaper
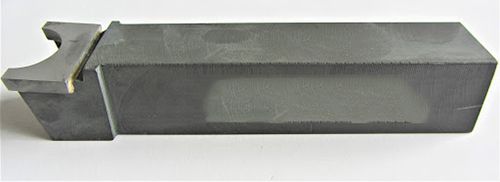
This type of turning machining uses profile turning tools, then the shape of the tool will be copied over the part, including vertical and horizontal profiles.
Advantages of CNC turning machining method in mechanics
- High precision in mechanical cnc turning is an advantage of this machining method, when CNC machines are used, the CNC turning process achieves higher accuracy and at the same time improves high productivity.
- The way to operate and manipulate on the lathe is quite simple and easy to implement.
- Turning is the most suitable method when machining round shaped parts.
- CNC lathes also have high applicability when in addition to turning, they can also be used in drilling, reaming, chamfering, grinding, grinding…
Disadvantages of the means method
- The machining method of cnc turning in mechanics depends heavily on the shape of the part, so for more complex products, the milling method will be selected.
- The productivity and accuracy of turning processing are also greatly affected by turning tools, processing materials, and lathe skills. fit.
HOT SELLING PRODUCTS AT IDEA:
-
ASSEMBLY JIG
Price: ContactAssembly JIG is used in assembling parts together to link product assemblies. JIG helps products achieve high accuracy and ensure technical requirements. Usually, assembly JIG is used to clamp product components for assembly, to position the parts to be assembled, to create profiles for welding, pressing, and air compression in the production process.
-
CNC MILLING MACHINING
Price: ContactWith CNC milling, we can accurately and detail process products according to orders from single units to mass production for FDI enterprises.
IDEA’s precision machining products have many varieties and diverse, meeting the needs of even the most fastidious customers. Our machines are imported from leading Japanese brands such as Mori Seiki, Makino, OKK, DMG CNC and multi-function machines, up to 120 types of machines suitable for all stages of mechanical processing. We can process many different sizes, can process beam frames up to 5m.
-
QUANTITY INSPECTION MACHINE
Price: ContactThe machine has the ability to automatically inspect the number of products on the line when packing, this helps manufacturers monitor productivity, and commit quantity and volume to consumers. In addition, it also helps to make statistics of productivity by shift, crew, month, quarter quick and in time.
All of these devices are designed in 3D, optimally simulating movements before manufacturing to ensure accuracy and reliable operation.
-
SORTING ROBOT
Price: ContactThe pick-and-sorter system is used to pick up products from input locations, and perform sorting according to predefined criteria and move products to other locations where is defined in the program.
-
CNC MILLING LATE MACHINING
Price: ContactWith milling and lathe, we can precisely machine complex, multi-tasking parts that require a combination of milling and turning.
IDEA’s precision machining products have many varieties and diverse, meeting the needs of even the most fastidious customers. Our machines are imported from leading Japanese brands such as Mori Seiki, Makino, OKK, DMG CNC and multi-function machines, up to 120 types of machines suitable for all stages of mechanical processing.
-
DEFECT INSPECTION MACHINE
Price: ContactDefects are also a serious error, which must be eliminated promptly before moving on to the next stage or before reaching the consumer. The machine is capable of automatically inspection for defects on products by applying modern image processing technology, ensuring high accuracy.
All of these devices are designed in 3D, optimally simulating movements before manufacturing to ensure accuracy and reliable operation.
-
6 AXIS ROBOT
Price: ContactThe 6 axis robot has a compact and flexible arm suitable for operations such as pick-and-place, precision assembly, parts transportation, and welding. The robot is light in weight and small in size, so it can be placed inside the processing machine, hung on high, and can work in narrow environments.
-
AUTOMATIC DEBURRING MACHINE
Price: ContactThe automatic bavia machine is widely used in production factories, is an important equipment to improve the efficiency of production activities, whose performance is superior to manual labor.
-
IMPURITY INSPECTION MACHINE
Price: ContactIf impurities exist or penetrate into products, it will cause great harm to manufacturers, especially in the field of food, drink and also in equipment and products requiring high safety. The machine is capable of automatically inspect different types of impurities, depending on the requirements of the customers.
All of these devices are designed in 3D, optimally simulating movements before manufacturing to ensure accuracy and reliable operation.
-
3 AXIS ROBOT
Price: Contact3-axis robot, XYZ robot is a specialized robot with high precision and speed, applied in the industry of manufacturing and assembling electronic components, automobiles and motorcycles such as applying glue to PCB circuits, or applying grease, glue to multi-point positions, difficult to manipulate, complex profiles on motorcycle gearboxes, circuit boards.
-
AUTOMATED GUIDED VEHICLES IGR – STA
Price: ContactAutomated Guided Vehicles IGR – STA is a very compact AGV for towing or carrying solutions.With simple modern design, this AGV will meet all of your expectations for various application with most reasonable cost.
-
PROFILE INSPECTION MACHINE
Price: ContactThe machine has the ability to automatically inspect all kinds of profiles, deformations, defects of the product caused by previous stages. The system is integrated by modern sensors and cameras to help detect errors immediately, prevent efflux and immediately prevent mass waste that can cause great losses to manufacturers.
All of these devices are designed in 3D, optimally simulating movements before manufacturing to ensure accuracy and reliable operation.